AUTOMOTIVE METAL FINISHING
AUTOMOTIVE ROBOTIC FINISHING
From nerf bars and exhaust tips, to billet grilles and truck bumpers, Acme serves automotive aftermarket manufacturers with cost-effective robotic finishing cells that meet production demands. With high repeat-ability, Acme systems perform operations such as cut and color buffing, polishing, and deburring that will create the stand-apart appearance features that help both new entrepreneurs and large industry veterans to gain more of this fast-growing, discretionary market. Materials include aluminum, steel, and stainless.
​
Acme robotic cells for automatic deburring or finishing wheels reduce unit costs, with highly-repeatable production rates using single or multiple 6-axis robots. Semi-automatic cells reduce manual finishing of wheels by 50% to 100%.
​
Aluminum Alloy or copper-plated wheels (cast or forged) from 14 in. to 24 in. OD, are finished on Acme robotic systems using flap wheels, buffs and other media, with up to 50 HP at the work spindle. Automatic compound systems are available for cut and color compound applications.
​
​
Applications Include (but not limited to):
​​
-
Wheels
-
Roof Rails
-
Step Bars
-
Grills
-
Bumpers
-
Crankshafts
-
Camshafts
-
Liftgates
-
Engine Blocks
-
Heads
-
Seat Frames
-
Transmission Component
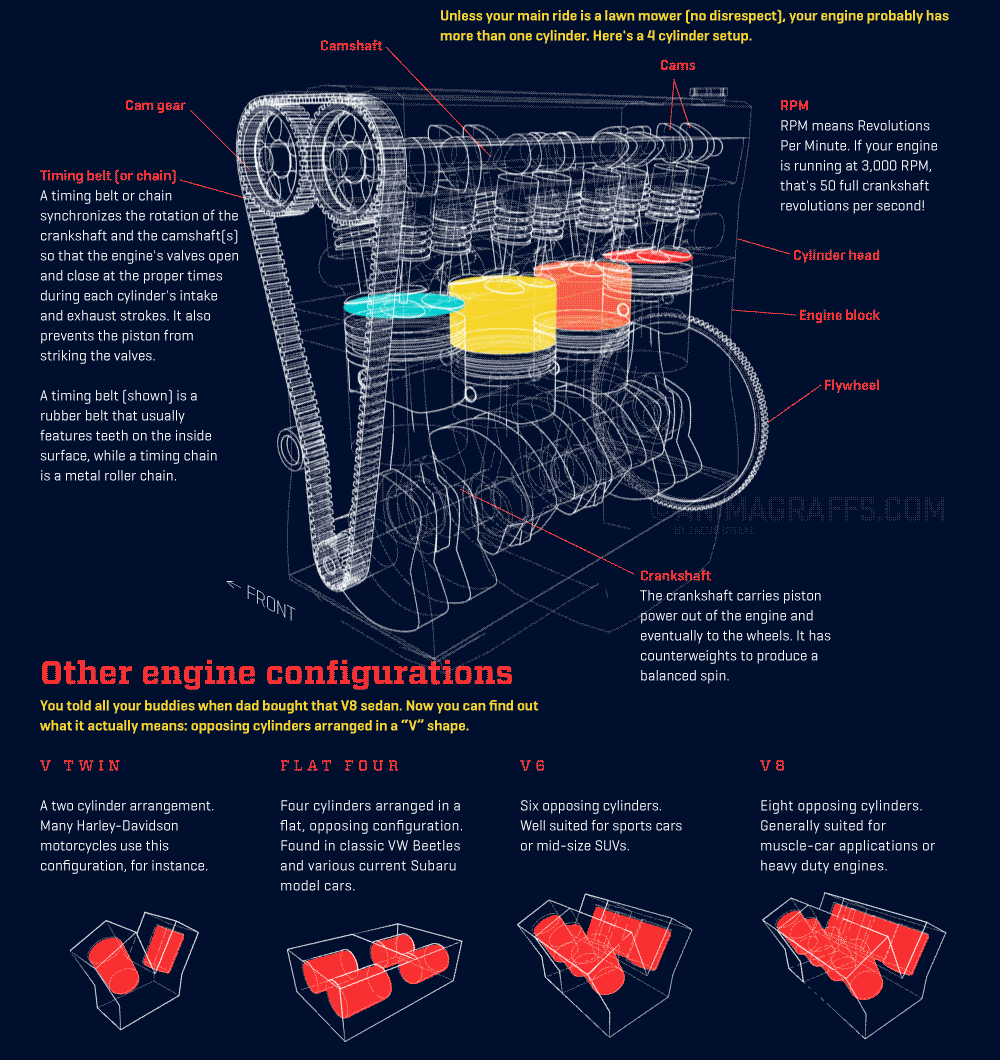
![]() | ![]() |
---|---|
![]() | ![]() |
![]() | ![]() |
![]() | ![]() |
![]() | ![]() |
![]() |
Processes include:
​​
-
Cut buff, color buff, satin finish, abrasive polish, soft polish, deburring and copper buffing
-
Backside and curbside finishing
-
Edge deburring and radiusing
-
Window finishing
-
Optional valves stem hole deburring with automatic part orientation
Wheel Windows:
– Polished with abrasive media by 6-axis robots
– Fixtured on dial-index table
O.E.M. and Aftermarket Wheel Manufacturers
Multiple Robotic Process for Polishing Aluminum Wheels. Both OEM and aftermarket wheels are processed on Acme robotic finishing systems, including two-piece wheels, aluminum truck wheels, billet aluminum wheels, and motorcycle wheels.
Cost Savings
Semi-automatic cells can reduce manual finishing of wheels by 50% to 100%. Switching from manual to robotic automation finishing alone can give you three to four times longer media life, as a result of contact efficiency (time on the part), constant work pressure, cycle time repeat-ability, and part path programming capability. Flexible, automatic force control, with variable-speed spindle motors, optimizes compliance (response and reaction) of the finishing heads to suit the operation.
Off-line programming and simulation (Roboguide) speeds up the program development process and increases utilization. Or, teach pendant programming, developed by Acme specifically for wheel finishing, can be used.
Universal tooling concepts developed by Acme for automotive and truck wheel applications reduce system design, build and operation costs. All equipment is built to RIA and CE specifications
Maintenance time and costs are minimized with on-line diagnostics and documentation. Troubleshooting can be performed via modem and/or internet, with Ethernet host support.
Media Life Management and Control
​
Automatic media wear compensation software ensures consistent performance throughout the life of belts and buff wheels by adjusting cell process parameters (such as cutting rate and force) to match the performance and lifespan of the media.
ROBOTIC METAL FINISHING VALUE PROPOSAL
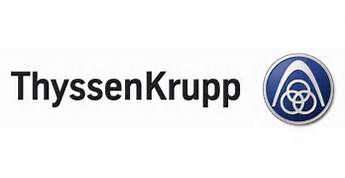


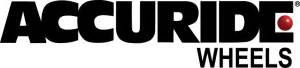

